為了解決鑄件中最後凝固位置的縮孔缺陷,冒口是最佳的選用方式,冒口的補縮是透過鑄件凝固時向內部提供熔融金屬來防止缺陷產生。為了使冒口有效補縮,放置的位置及大小就非常重要,這樣才能有足夠的熔湯來補償收縮。在FLOW-3D CAST中,已經開發出兩個新工具來幫助設計無缺陷鑄件的冷卻和冒口系統,預測最後的凝固位置和計算熱模數。
最後凝固的區域
最後凝固的區域直接標記出鑄件中最後凝固的位置以及可能形成收縮缺陷的位置。 儘管這些位置可以從凝固順序的演變或凝固時間中得到,但始終首選使用更直接的方式來可視化它們。
一種特殊類型的固定顆粒用於識別和可視化最後凍結的位置,稱為“熱點”。 使用凝固模型時,將自動輸出此結果。 如圖1所示,在相鄰的區域的熔湯變為固態時中心位置還未凝固就會自動生成熱點粒子來標示。

除了確定最後凝固的位置之外,這些粒子還具有其他屬性,可用於確定這些位置中的收孔缺陷的發生可能性和大小及凝固時間,熱點ID和熱點大小。凝固時間顯示完全固化的時間點。熱點ID顯示了熱點固化的順序:ID 1是第一個熱點,ID 2是第二個熱點,依此類推。最後,熱點大小可通過以下公式計算:

其中:
hsm(i)是粒子i的熱點大小
t0是粒子位置處的凝固時間
νliq(t)是在時間t處包含粒子的液體區域的體積
圖2顯示所連接液體區域的體積如何隨凝固時間的變化。然後將計算的量標準化,使所有熱點幅度的值都在0和1之間的範圍內。這允許鑄件內不同熱點對孔隙形成的潛在影響進行簡單的比較分析。值越高,凝固過程中連接的液體區域越大,表示在最後凝固的位置出現縮孔缺陷的可能性越大。
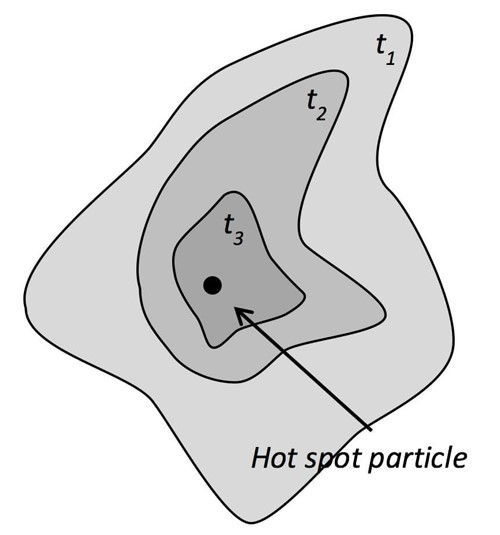
熱模數法
熱模數法是常規冒口設計中最受歡迎的方法之一,特別是對於鋁合金和鋼鑄件。對於給定的鑄造零件,其模數定義為:

其中:
V是鑄件的體積
A是鑄件的表面積
對於常規形狀(例如球體或塊)而言,鑄件的幾何模數很容易計算。任何比這更複雜的工作都需要通過常規形狀來繁瑣地近似鑄造段。此外,幾何模數方法嚴格依賴於鑄件的幾何形狀。實際的鑄件使用冷鐵和保溫套來控制凝固過程。這些特徵在幾何模數方法中被忽略。為了自動進行模數計算,並考慮到與冷卻,包溫套和其他模具變化相關的熱效應,通常在冒口設計中使用一種稱為熱模數的創新方法。
對於熱模數方法,首先進行鑄件的凝固模擬。一旦模擬完成,就可以根據Chvorinov的規則從凝固時間計算出整個鑄件的等效模數。使用此方法計算的等效模數稱為熱模數。可以使用與幾何模數相同的方式來設計冒口系統。
Chvorinov的規則給出了凝固時間之間的關係,其模數可以寫為:

其中:
t是鑄件凝固時間
N是一個常數(通常等於2)
B是模具常數可以使用以下公式計算

其中:
ρm是金屬的密度
Tm是金屬的熔化或凝固溫度
T0是模具的初始溫度
k是模具的導熱係數
ρ是模具的密度
c是模具的比熱
L是金屬熔化的潛熱
cm是金屬的比熱
Tpour是金屬澆注溫度
在設計鑄造製程時,通常以這樣的方式選擇冒口,即冒口的凝固時間長於相鄰澆鑄段的凝固時間,以便有效補料。 根據Chvorinov的定律,凝固時間與鑄件的模數成正比。 因此,當比較凝固時間時,模數可以直接比較。 由於模數僅僅是幾何量,因此模數的比較使設計任務更加簡單。金屬鑄造工程師可以設計具有更大模數的冒口,以確保正確地補料給零件,而無需考慮實際鑄造工藝的細節。
冷卻和冒口系統設計中的應用
由Flow Science China提供並討論了使用此功能對半汽輪機汽缸,如圖3,進行重力鑄造的冷卻和冒口系統設計。 零件的外部尺寸為2.83×2.34×1.10米,總體積約為0.95立方米,如下所示。 鑄造材料為碳鋼,澆鑄溫度為1530°C。

首先,對沒有冷卻和冒口的鑄件進行凝固模擬。 目的是確定熱點位置,並確定冷鐵和冒口的位置,以及冒口的尺寸。
下圖顯示了凝固時的熱點粒子,分別以凝固時間、粒子ID和熱點大小來顯示。從這些圖直接看出熱點位置和形成縮孔缺陷的可能性。根據鑄件的幾何特徵,放置冒口的位置很容易確定,如圖4右側所示。但是,底殼上有一些熱點,不適合放置冒口。為了防止這些位置的縮孔缺陷,可以使用冷鐵來改變凝固方式,以驅使最後的凝固位置在冒口區域。
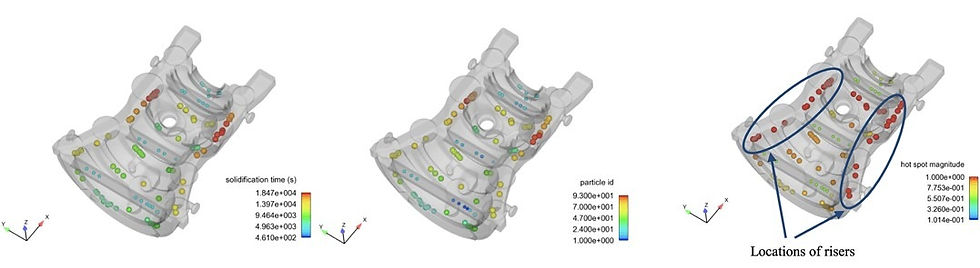
計算出的熱模數顯示在右側。較大的值與最後凝固位置一致。此外,熱模數可用於確定熱點位置的冒口尺寸。確定冷鐵和冒口後,將運行第二次凝固模擬,以驗證冷鐵和冒口的設計。