翻譯自《美國現代鑄造雜誌》
發熱冒口在鑄鐵中的應用越來越多,一種新型發熱冒口有助於鑄造廠更有效的設計澆注系統。
在重力鑄造中,發熱冒口的使用是非常廣泛,但對於工程師在設計上來說是一個抉擇,因為冒口的尺寸和模數夠大能有效避免縮孔,但成本就必須增加,而且會增加回爐料。鑄件複雜程度的不斷提高,進一步增加了開發需求。高發熱冒口系統比傳統的砂冒口更節省空間,效率更高,因此變得越來越重要。
冒口系統可分為保溫冒口和發熱冒口兩種。對於保溫冒口是透過一個熱導率明顯低於砂模熱導率的冒口,可以延長冒口中鐵水的凝固時間。因此,鐵水保持液態的時間更長,可用於連接處來進行補縮。通過使用發熱材料,可以減小冒口的尺寸。因此,當冒口鐵水溫度超過起燃溫度時,發熱材料會發生放熱反應。鐵水被釋放出來的熱量加熱,因此保持液態的時間更長。因此,發熱冒口系統是非常好的選擇,可以用更少的體積為鑄件提供更長時間的液態金屬液。
雖然過去使用簡單的幾何模數計算公式,但現在鑄造廠可以利用鑄造模擬來預測熱點位置和凝固形態等,來幫助冒口的設計。模流分析是尋找有效解決方案的工具,特別是在選擇和確定冒口的尺寸方面。電腦輔助設計和鑄造模擬應用的技術日益增長,鑄件的需求已經一次又一次地得到解決;同時,這些方法已經成為鑄造廠大多數標準開發過程。對普通和保溫冒口系統的數值描述是準確的,可以得到可靠的結果。然而,到目前為止,使用發熱冒口系統的模型還不能足夠精確地預測過程,導致實際中冒口的尺寸過大,形成高成本的解決方案。在模擬軟體中盡可能準確地描述發熱冒口材料的燃燒行為,因為發熱冒口現在是鑄鐵件中最常用的冒口類型。
該模型可以準確地描述冒口頂部的燃燒行為,即頂部能量釋放的時間和空間過程。
1. 目前技術
發熱冒口材料包括鋁和氧化鐵。因為鋁比鐵對氧有更高的親和力,這些材料反應會強烈放熱。
氧化鐵和鋁反應時產生大量熱量生成氧化鋁和鐵。(鋁熱法,或金施密特法Gold-schmidt Process)。
Fe2O3 + 2Al → Al2O3 + 2Fe……………………………………… (1)
這一反應只會在一個特定的起燃溫度之上進行,而這個溫度是由於金屬液填充砂型而達到的。在大多數冒口系統中,發熱材料從冒口內部徑向向外燃燒。燃燒時間取決於冒口的幾何形狀和材料的特定燃燒速度。
鑄造業界不斷開發出更多的冒口種類和組合,例如由保溫和發熱材料組合而成的混合冒口。
到目前為止,發熱冒口系統僅在模擬軟體中進行簡單描述,整個冒口體積被分配在一個規定燃燒時間內不斷釋放的熱量。對於用戶來說,因為這取決於冒口的幾何形狀,確定發熱量已經足夠困難了,更難確定燃燒時間。
這種簡化的建模形式可能會導致模擬結果與實際情況嚴重落差,導致冒口尺寸過大。至今為止,在鑄造模擬中還沒有考慮到材料性能在未燃燒和燃燒狀態下的變化。
實驗研究首先進行熱物理性質的測量,以獲得冒口材料的資料。對每個時間單位具有規定熱量的樣品進行加熱,並連續測定材料特性。在這些測量過程中有一個困難點,發熱反應引起的高水準動態性一旦達到起燃溫度,材料就會自動燃燒,不再跟隨測量系統的溫度。只有在這些實驗中才能可靠地確定未燃燒狀態下的材料性能。因此,燃燒過程中和燃燒後的燃燒行為和材料性能,最初是不準確或未知的。
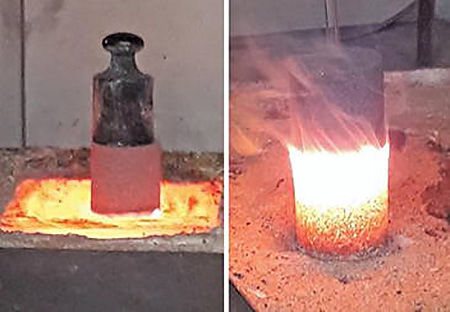
更精確地研究燃燒行為是有必要,所以建立了一個實驗來測試發熱材料(圖1)。使用發熱材料製作了兩個試樣 (D=50 mm,H=50 mm),一個放在另一個上面。點燃下部試樣,研究兩個試驗品的燃燒行為。這種設置可以觀察和理解燃燒過程的進展。然後將燃燒行為的時間和過程與模擬進行比較(圖2)。

在對試驗品燃燒性能進行研究的基礎上,進行了呋喃砂型鑄造試驗。在鑄造實驗中,利用金屬液填充呋喃砂型中的發熱冒口,測定了澆注溫度曲線。為此,在發熱材料、型砂和金屬液中放置單獨的熱電偶,以確定溫度變化。
一個熱電偶被放置在冒口的金屬液中。另外兩個位於冒口內,兩個位於型砂中(圖3)。冒口內填充熔化的GJS 400進行測量。
重複進行測量,盡可能提供具有決定性的重複性和溫度曲線。用三種不同尺寸的冒口試樣(0.95 cm、1.5 cm和2.7 cm)重複試驗,在許多可能的不同因素(例如,不同的測量位置、材料或密度),並在較廣泛的實驗要素下檢查模擬模型。根據記錄的溫度曲線計算標準差,並與模擬結果的測量值進行比較(圖4)。
可以看出,模擬結果的溫度曲線大部分位於計算的標準差範圍內。由此可以得出,模擬結果與實驗結果之間的溫度曲線偏差在測量精度範圍內,並且可以準確地表示出所實現的發熱冒口行為模型。
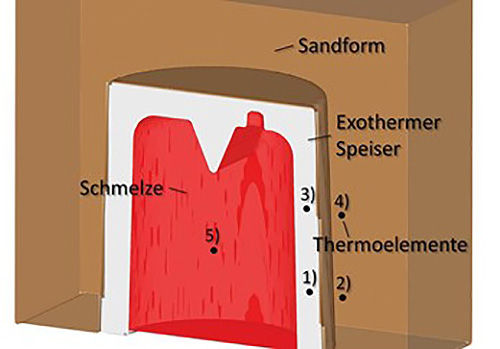
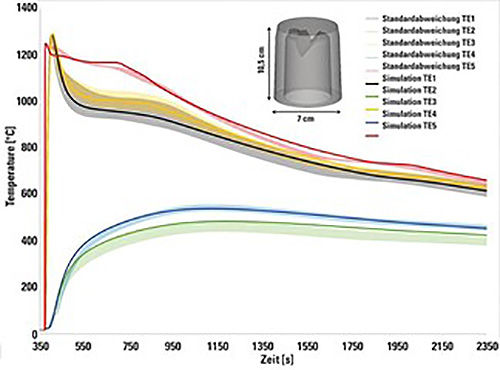
2. 新模型
新模型盡可能準確地模擬實際情況。冒口不被視為一個在任何地方都表現相同的放熱量,而是將計算網格的每個單元分別處理。當冒口的網格單元達到起燃溫度時,就會觸發放熱反應,並根據計算的函數釋放熱量。網格的溫度升高並加熱相鄰的網格,就像連鎖反應一樣,因此它們也達到了起燃溫度。透過這種方式,在冒口內顯示了真實的燃燒行為。放熱反應發生後,冒口材料的性質發生變化,產生保溫效應。在模擬中,每個單元的冒口的材料特性也與燃燒水準相對應。因此,未燃燒和已燃燒材料的熱物理性質不同,對發熱材料燃燒過程中的溫度分佈有進一步的影響。燃燒過程的不同階段如圖5所示。當金屬液將材料溫度升高到高於起燃溫度時,冒口開始放熱反應。然後,這種材料會自動燃燒並釋放熱量來加熱金屬液。
放熱反應結束後,由於保溫性能的原因,會出現“餘熱”。因此,可以保持放熱反應的高溫,並且冒口可以長期向鑄件提供金屬液。
與以前的定義相比,一個主要的附加值是,一個材料,其所有參數都是已知的,可以在資料庫中列出具有普遍有效性的。在模擬過程中,未知值(例如整個冒口的燃燒時間)會自動出現。在軟體中實現了冒口資料庫(圖6)。資料庫包含發熱和保溫冒口的冒口資料。根據模數計算,可以快速有效地選擇合適的冒口,並檢驗其效果。


3. 驗證
使用保溫冒口的案例研究如圖7所示。孔隙率分析表明,冒口只能補償鑄件的收縮。由於凝固時間長,保溫冒口不能使金屬液在高溫下保持足夠長的時間,在冒口區域形成一個臨界的二次縮孔。儘管缺陷位於冒口內,但它仍然非常不穩定,因為製程參數(如鑄造材料的化學成分或鑄造溫度)的波動會導致部件中的孔隙率發生變化,從而導致鑄件報廢。儘管製程參數在公差範圍內,但仍存在一些缺陷部件。選擇發熱冒口,並使用新的模擬模型對其進行尺寸標注,以找到一個穩健有效的解決方案。未觀察到二次縮孔的形成;液體足以在凝固完成之前將部件壓實填充。由於採用了更有效的操作模式,可以選擇更小體積的冒口,減少30%的金屬液體積,從而減少不必要的回爐料。由於冒口對製程相關波動不敏感,且能可靠地防止鑄件內部的缺陷,因此可以透過使用發熱冒口實現穩健的解決方案。
